Machine learning unlocks capacity, reduces costs and improves quality in modern manufacturing
An incredible example of machine learning in practice, providing our client with more than $600,000 of annual savings.
Machine learning (ML) and artificial intelligence (AI) are more common in modern manufacturing than most people realize—and they’ve already revolutionized manufacturing. Let’s dig a little deeper to see how applying machine learning can unlock capacity, improve quality and reduce costs.
What is machine learning?
Machine learning is a category under the umbrella of artificial intelligence. Machine learning applications are applied in the automation, mechanization, and integration of industrial process control, automated assembly, packaging, and warehouse logistics operations.
Machine learning provides harmonization within the manufacturing environment. Through analyzing feedback, instrument data and analytics, individual work cells and processes can adapt to changing conditions in real-time.
Machine learning is like creating the perfect harmony.
I often associate machine learning with music. Each instrument (or process) has a beautiful and specific sound. A conductor listens to the individual instruments and brings them together in perfect harmony. Machine learning makes the harmonization of processes possible, which produces greater results.
“Our client’s four-hour downtime and $45,000 investment provided more than $600,000 of annual savings by reducing giveaway alone. “
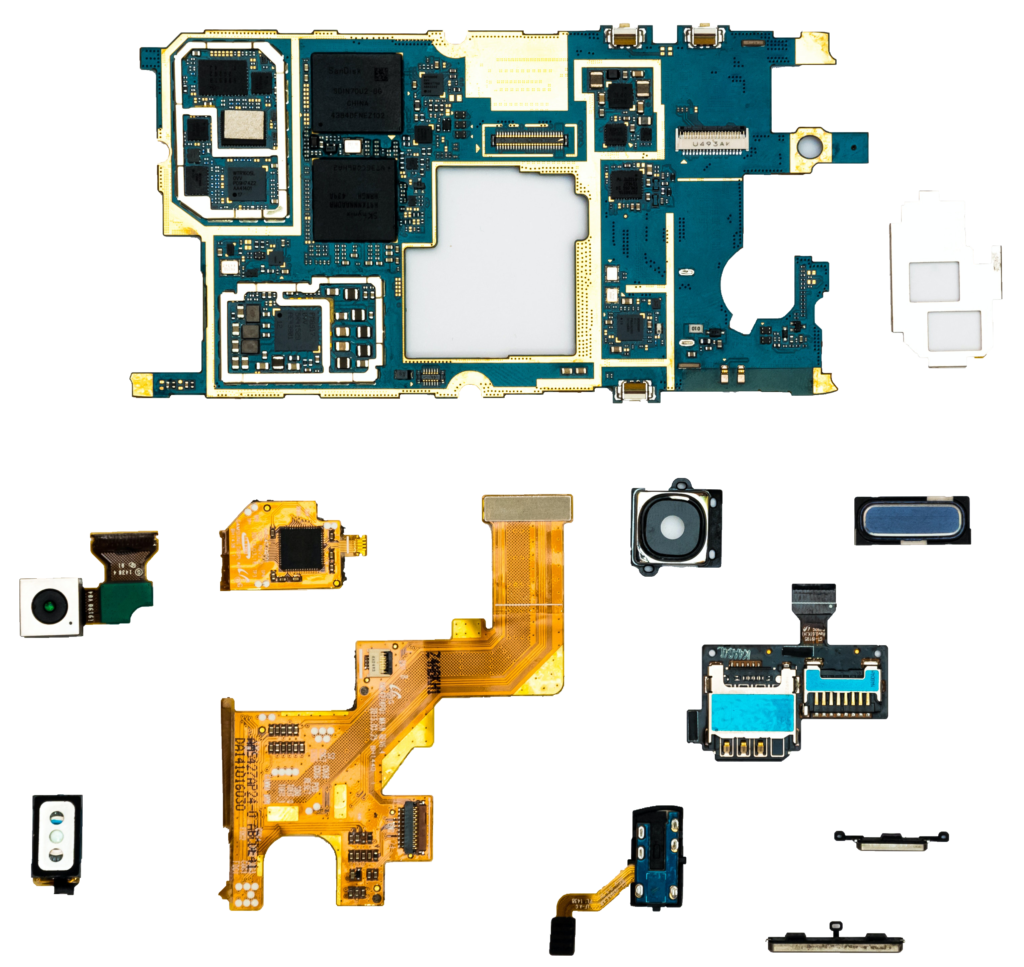
How does machine learning improve quality?
A common example of how machine learning is used across many industries is the interface of a continuous web to intermittent motion for converting. In baking and snacks, we see this as the output of a dough sheet that is converted into pieces for portioning and packaging.
This sheeting process—creating a continuous web and converting it to individual pieces—often requires intermittent motion or a dwell of a continuous process. Product attributes need to be controlled during manufacturing—density, weight, rate, surface conditions, and energy imparted on the product are all controlled with the goal of adherence to tolerances, and delicious snacks that look and taste the same.
Previous methods, like mechanical solutions, provided accumulation directly coupled to the process. Servo motor applications provided improvements with adjustable ratios, accelerations, and deceleration capabilities. But by applying machine learning algorithms, we can now close the loop based on product dynamics—providing appropriate slip and gain as material transitions through accumulation and into conversion.
How does BC Automation leverage machine learning for our clients?
Recently, a client came to us looking for improved quality and in turn, improved savings on their finished goods. We provided a simple retrofit to the in-feed festoon assembly control algorithm. We applied our solution on top of the existing equipment and control system. With the addition of two sensors, and our layered adaptive process control model, we provided immediate stability.
Our client’s four-hour downtime and $45,000 investment provided more than $600,000 of annual savings by reducing giveaway alone.
The tightened finished goods tolerances and improved quality that resulted from this project provide ongoing and immeasurable benefits for our client. For our part, this application led to accelerated adoption of this application across every production line in their system.